The most advanced carbon bikes
TIME Bicycles founder Roland Cattin set a bold path with his inspired selections of unique manufacturing techniques and European production. For him, the bottom line was not financially motivated and had everything to do with seeking premium performance.
It’s a tribute to his vision that TIME still leads the way after more than 30 years and is widely known for making the finest carbon bikes in the world.
TIME: Perfection in every strand
Unique technologies, unparalled expertise
The processes we use at TIME are unique in the bicycle industry. Not because they are unproven or secret (they are fairly common in aerospace and high end automotive) but because they’re expensive and require a different level of commitment, equipment and training.
TIME is fortunate to have taken this road from the beginning, compiling decades of skill and unique engineering experience. With this unique “outsider” perspective, we acknowledge that industry-standard techniques can certainly produce a light, reactive and comfortable frame that rides well, but in the context of composites engineering, TIME’s products are superior. This opinion isn’t ours alone; it’s shared by carbon engineers the world over – our manufacturing processes yield a product that is safer, smarter and stronger.
Why our bikes are better
Both the Braided Carbon Structure and Resin Transfer Moulding processes allow TIME to control every individual strand of carbon used in the construction of a frame. With more than 30 years experience of TIME have elevated the standard in creating carbon fibre to match the level found in Formula One.
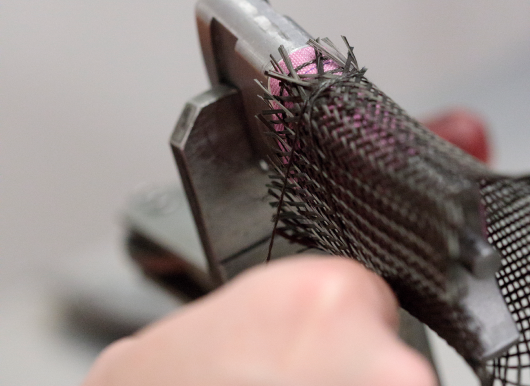
BCS
Braided Carbon Structure
Braided Carbon Structure is our term for the weaving of fibres into complex bi-directional ‘socks.’ These tubes are easy to tune with different materials – TIME currently choses from 16 filaments to perfectly tailor our layups. This process allows something that is unheard of in the cycling world; continuous, unbroken fibres that run the full length of a structure.
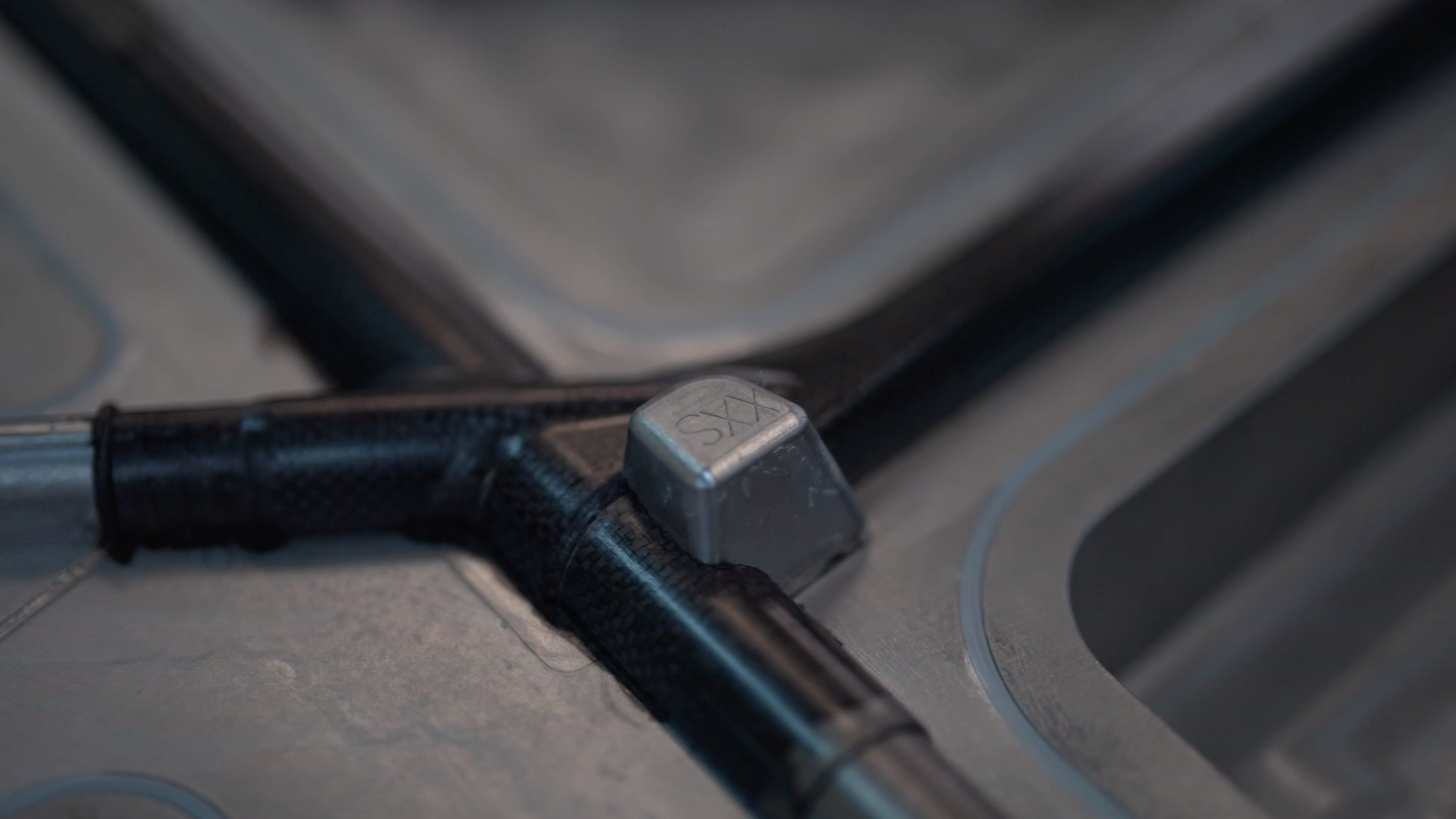
RTM
Resin Transfer molding
Resin Transfer Molding is the best way to minimize defects in the composite structure. By injecting resin under high pressure between rigid external and internal molds, air pockets are pushed out and voids between layers are eliminated.
Compression molding technology
We utilise forged carbon in many parts of the frame to increase strength and longevity. Our CMT forged carbon seatpost heads and dropouts have 20x the fatigue life of steel or aluminum and are lighter than both. In addition, the 60% fiber mix eliminates propagation of cracks.
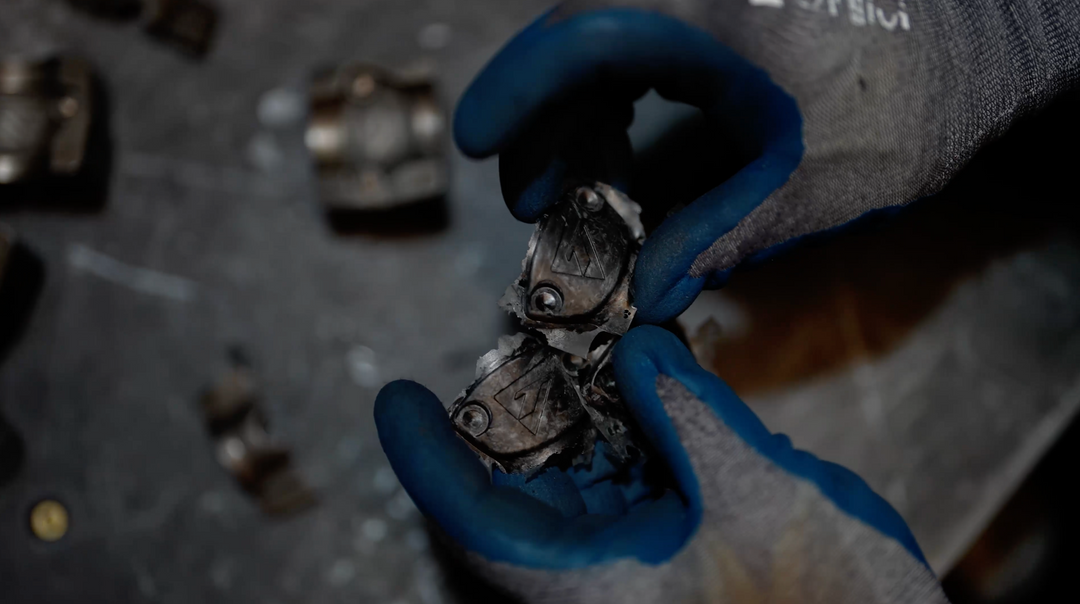